Articles
on Mass Flow
Flow Research is
proposing a first-ever Mass
Flowmeter Series with a Core Overview Study, The World Market for Mass Flow
Measurement and
in-depth studies on three types of flowmeters that measure mass flow
directly:
·
The
World Market for Coriolis Flowmeters, 7th Edition
·
The
World Market for Thermal Flowmeters, 3rd Edition
·
The
World Market for Mass Flow Controllers, 4th Edition.
Each of these separate
studies in the series is interesting in its own right, but the Core Study
is composed of high-level results from each of the studies to give a
comprehensive picture of the entire mass flowmeter market. We also include
data on multivariable mass flowmeters in this Core Study.
Core Study Goals
This
executive-level study will determine the size of the entire mass flowmeter
market in 2022 and forecast market growth through 2027. Segmentation will
include total worldwide market size broken down by eight geographic
regions and the basic mass flow technology types: Coriolis, thermal, MFC
and multivariable flowmeters.
The study has multiple objectives:
·
Show worldwide market size and shares for the mass flow market in
2022 for Coriolis, thermal, mass flow controllers (MFCs), and
multivariable flowmeters
·
Forecast mass flowmeter market growth through 2027
·
Share top-level data about each of the types
·
Segment data both on a worldwide basis and for each of eight
worldwide regions
·
Discuss market forces and suggest strategies
for selling into the mass flowmeter market
About Mass
Flow
While the majority of flowmeters
measure volumetric flow, three types of flowmeters measure mass flow
directly. These three types are Coriolis, thermal, and multivariable
flowmeters. This atudy discusses the reasons for measuring mass flow,
and then looks at the advantages and disadvantages of Coriolis, thermal,
and multivariable flowmeters. Another type, mass flow
controllers, both measure and control the flow. Mass flow
controllers are used both in the semiconductor industry and in industrial
markets.
To
learn more about multi-tech, go to:
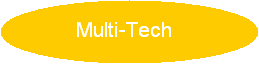
Coriolis flowmeters
Coriolis
flowmeters use fluid momentum to measure mass flow directly. The
fluid enters the meter and passes through one or more vibrating tubes and
accelerates as it reaches the point of maximum vibration. As
the fluid leaves this point, it decelerates. This causes an
oscillating motion in the tubes. The Coriolis meter measures
this oscillating motion, and mass flow is directly proportional to the
amount of oscillation.
Coriolis
flowmeters are the most accurate meters. Their main limitations are
line size and cost. Over 67 percent of Coriolis flowmeters are
used on line sizes of two inches and less. Coriolis meters become
very large and unwieldy, especially in sizes above four inches. Cost
also increases with size. Even smaller size meters are
generally more expensive than other comparable new-technology flowmeters. Users
who are considering Coriolis flowmeters need to balance their need for
accuracy and reliability against purchase price. Some users select
Coriolis meters despite their higher initial cost, because low maintenance
requirements reduce their cost over the life of the meter.
The
high accuracy of Coriolis meters – up to 0.05 percent – is one of the
major reasons for their continued growth. Companies that need flowmeters
for custody transfer, or want highly accurate measurements in terms of
mass, have good reasons to select Coriolis flowmeters. They find that
despite a relatively high price tag, Coriolis flowmeters can provide a
good return on investment.
Thermal
flowmeters
Thermal
flowmeters are among a small group of fluid measurement technologies that
can generate a mass flow measurement independent of additional component
technologies. Mass flow data
is generally considered more
useful
than volumetric data for many applications - such as custody transfer of
hydrocarbon fluids - and can offer higher repeatability, a level of
measurement certainty highly valued by process and quality control
managers alike.
Thermal
flowmeters measure mass flow quite differently from Coriolis flowmeters.
For example, instead of using fluid momentum as Coriolis flowmeters do,
thermal flowmeters make use of the thermal or heat conducting properties
of fluids to determine mass flow. While
most thermal flowmeters are used to measure gas flow, some also measure
liquid flow.
In contrast,
other flowmeter types that can also produce a mass flow result do so with
the addition of pressure and temperature sensors.
Mass flow is then computed from the volumetric flow, and the
temperature and pressure variables. Multivariable
differential pressure and vortex flowmeters can both be used in this way
to compute mass flow.
Mass
Flow Controllers (MFCs)
Mass flow measurement, which measures the mass of a fluid
independent of pressure or temperature, is more reliable and offers a
higher accuracy and repeatability than volumetric flow, which measures the
volume of a gas or liquid occupying a pipe. This difference is
particularly important for gases, which shrink or expand in volume with
changes in pressure or temperature, but whose mass – the number of
molecules – stays constant.
Fortunately,
a mass flowmeter can easily provide flows in volume by adding the volume
(including the pipe diameter) to the calculation. Conversely, some
volumetric flowmeters e.g., multivariable vortex and differential pressure
flowmeters – can indirectly provide mass flow by also measuring
temperature and pressure and computing the mass flow.
MFC
technology types are thermal, pressure, Coriolis, and ultrasonic.
Because MFCs are used both to measure and to control fluid flows,
the study will identify their use by fluid type.
We will also quantify the presence of MFCs in significant
industries and applications, including semiconductor and industrial.
What are the Advantages of Multivariable
Flowmeters?
Multivariable
flowmeters measure mass flow by combining volumetric flow measurement with
density measurement. Density is usually measured either by consulting
a table, or by dynamically measuring pressure and temperature. This
is called an inferred method, because a formula is used to compute mass
flow. The main types of multivariable flowmeters are
differential pressure (DP), vortex, and ultrasonic.
One main advantage of multivariable
DP flowmeters is that only one process penetration is required to get
three process readings: flow, temperature, and pressure. This reduces
the chance of fugitive emissions, and also the number of leak points. Another
advantage of multivariable DP meters is that users who are already
measuring volumetric flow with a DP flowmeter can upgrade to a
multivariable DP meter with a minimum of changes.
One disadvantage of multivariable
flowmeters is that accuracy levels are not as high as accuracy levels of
Coriolis meters. This is due to the number of variables
involved, and to the fact that it is an inferred method of computing mass
flow. On the other hand, the purchase price of multivariable
flowmeters is substantially below that of most Coriolis meters.
|